The expectations that manufacturers have of their OEE software partners continue to evolve and become more demanding. Software tools that merely report and display OEE performance are no longer sufficient for the most progressive manufacturing businesses. If you are in the process of researching and selecting an OEE software partner for the future make sure you get the best OEE solution from the best OEE software supplier for your business. Below, I propose 10 tough questions to ask your OEE Software Supplier prior to making your final selection.
I hope you find them helpful.
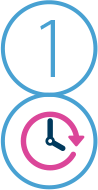
How long will it take to install the OEE software?
You should expect that software installation and configuration on a server should be fairly routine, but what happens once the software is installed ? How long to get the equipment connected ? How long to verify the data ? How long to ‘fine-tune’ the configuration ? How long to train users on the software? How long to see real results? And of course, how long before the software pays for itself?
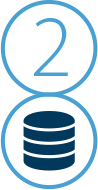
How much data can you collect automatically, without user involvement?
You should expect that software installation and configuration on a server should be fairly routine, but what happens once the software is installed ? How long to get the equipment connected ? How long to verify the data ? How long to ‘fine-tune’ the configuration ? How long to train users on the software? How long to see real results? And of course, how long before the software pays for itself?
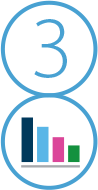
How can I present the OEE results in non-technical terms that are familiar to the manufacturing teams?
Once all this data has been collected, how do you present it? How do I avoid having to deal with the technical terminology of the alarms presented by the equipment? Dashboards are all in vogue, but how do you know that the contents of the dashboards are fit for purpose? Can I have different dashboards for different purposes – e.g. a Management Dashboard, a Production Dashboard, a Daily Meeting Dashboard, a Maintenance Dashboard, a Quality Dashboard? Can I create and configure my own dashboards, and how can I use these dashboards to collaborate with colleagues to drive operational improvements?
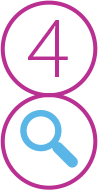
How can I analyse all this OEE data quickly and easily?
Presenting data is not the same as analysing data. You need to be able to find information amongst the data, analyse trends, spot anomalies and identify differences in performance across machines, lines, products, shifts, teams, etc. How easy is it to query the data? Do I need a reporting tool? Do I need to build queries? How much drill-down can I do on each chart? Can I analyse data from the highest level down to an individual event on the line?
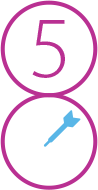
How will the software quantify what improvements I can achieve and pinpoint what I need to do to deliver these results?
Even with the slickest presentation of data it can sometimes be difficult to quantify improvement opportunities. Just because an OEE loss is at the top of the Pareto Chart doesn’t mean it’s the loss with the most potential for improvement. So, how do I identify the top opportunities? And when I have identified these opportunities how do I know, with certainty, what I need to do to deliver on these opportunities? How good is the software at telling me exactly what I need to work on in order to deliver results?
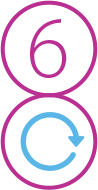
How good is the software at telling me exactly what I need to work on in order to deliver results? How will the software help me make improvements in real-time on the production floor, or is it just for historical analysis?
It is not sufficient for an OEE software system just to report on historical losses. The best performing businesses deal with OEE losses as they happen, not after the event. How can the OEE software solution help reduce the impact of losses in real-time? What can the software do to help Line Operators minimise the impact of a downtime event as it happens? Can losses be predicted and hence avoided?
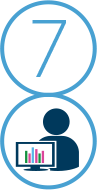
Q7 How can the software maintain and assess performance on the lines, or is it just for measurement?
All too often technical intervention on the equipment on the production line can cause frustration. Technical personnel, often under pressure, may not have the time to fully resolve a problem on the line. So their focus is on getting the line back running and to move on to the next problem. But can the software determine that a technical intervention on the line has been successful, or not? Can it monitor the progress of resolution to a performance problem on the line? Can it escalate an issue if it is taking too long to resolve? And, can the software assess the effectiveness of the Preventive Maintenance Program?
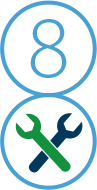
What about preventing problems – can the software do this?
Collecting data, measuring performance and presenting and analysing data is all very well. But it’s too late when the problem has happened and the line has suffered an impact to its OEE performance. What about predicting problems? What if you could foresee an event that would impact your OEE performance and you were able to use this foresight to avoid the problem? Wouldn’t you expect the best OEE Performance Management Software to be able to do this for you? Make sure to ask if it can!
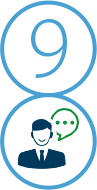
If I have a problem, who will I get to talk to?
If you have a problem with the software who will you be dealing with in the software provider’s office? Will you be dealing with a call centre? Will you have a dedicated Customer Success Manager? Will you have access to the software development team? Will your provider be able to make the changes you require, or will these have to be authorised and resourced by a remote development team? And if you have an urgent or important request will you have access to the senior management team and will they give you the mind share you require?
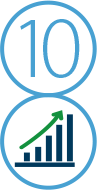
Aside from the software, can you help me deliver measurable performance improvements?
And finally, leaving aside the software itself, can your software provider help you to use the software to deliver the improved business results that you require? Will they help you work on technical, production, operational, quality, people and cultural problems to drive OEE improvement? Do they have the experience to work with your internal teams and collaborate to deliver the impact you need? Are they able to coach your middle and senior management on the techniques of Operational Excellence and Overall Equipment Effectiveness?
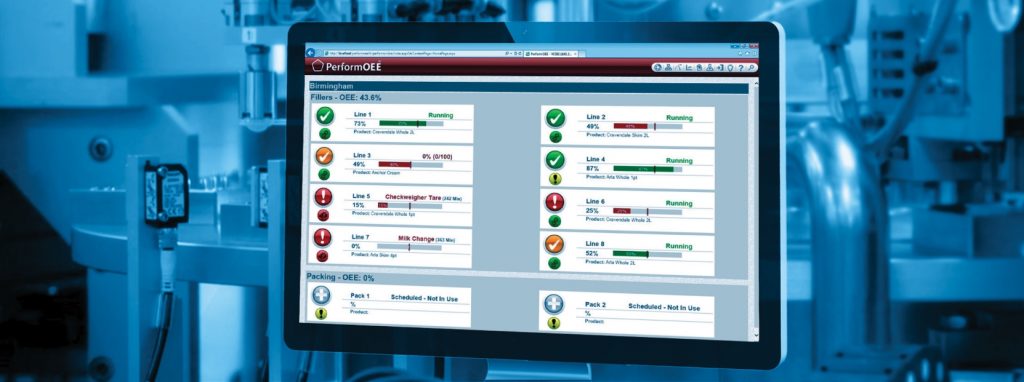