Every organization struggles with operational and other inefficiencies. Efficiency issues are often dependent on how efficient the company is at aligning production with demand and establishing continuous flow in its production process. Meeting customer demand is an important factor in delivering consistent, long-term value and making the company sustainable. The concept of Takt Time is at the core of production efficiency and helps ensure customer demand satisfaction.
What is Takt Time, and how does it affect customer demand? A company can use Takt Time to improve lean production operations, reduce waste and bottlenecks, and preserve the work process “heartbeat”.
What is Takt Time?
Takt Time is far from being a new concept, as it first appeared in post-WWI Germany. It resurfaced again in Japan during WWII before being embraced by Toyota to introduce the just-in-time production process.
Takt Time is a value enhancing tool to establish the pace of the production process according to customer demand.
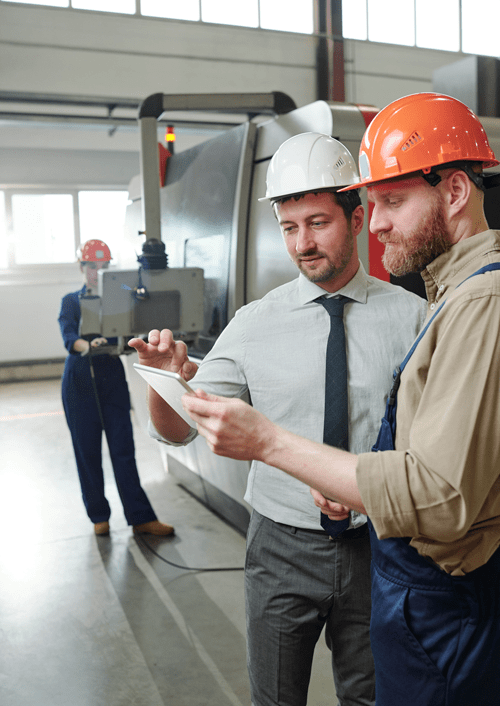
Definition - Takt Time as Production Time Rate
Takt Time refers to the rate at which a company needs to produce products for production to be aligned with customer demand. Aligning production rate with the demand of customers is important to create customer satisfaction, prevent waste, and maintain efficiency.
In other words, Takt Time provides a calculation of the production rate that addresses the following questions:
- What is the optimal production rate in order to deliver products in time?
- What is the most efficient production rate to make the right quantity of units and meet customer demand?
- How to take account of necessary breaks during the production period (hour, day, week, or month) and keep customers satisfied?
The Concept of Heartbeat or Beat Pace from Germany
The terms “Takt Time” come from the German word Taktzeit:
- Takt means pulse or beat, as in heartbeat or music beat.
- Zeit = time
Based on this, Takt Time is often described under the terms “heartbeat of the work process”.
In German, the terms are combined into one to describe the production time divided into multiple Takt stations; in other words, how long is needed to make the individual parts of a single product and meet the demand of customers.
Toyota Explains Available Production Time
In Japan’s WWII, German engineers trained Mitsubishi in the important principles of Takt Time. But it was only post-1945 that Toyota CEO began to blend continuous flow and mass production techniques.
The founder of Toyota Production System (TPS) describes Takt Time as:
“Takt is the length of time […] it takes to make one piece of the product […] obtained by dividing the available production time per day by the required number per day.”
Toyota Production System
Over time, the Takt Time techniques deployed throughout TPS became popularized through lean production.
Why is Takt Time Important?
Production efficiency relies on companies being able to run manufacturing processes at the pace set by Takt Time. Once you’ve got Takt Time calculated, it provides crucial benchmark metrics to run the production process against.
This means the manufacturing time is specifically aligned to meet customer demand as quickly as possible. The Taktzeit strategy is to design it so production can run at a sustainable, consistent pace to satisfy the demand of customers and prevent waste.
Takt Time Calculation
The Takt Time formula is calculated by dividing the available production time by the customer demand.
The Takt Time Formula
Available production time divided by customer demand volume (the order of units or products)
Both metrics in the Takt Time formula are expressed in the same period of time, aka hour, day, month, week, etc.
For example, let’s assume that a customer passes an order for 60 units per day. If the team works 24 hours a day with 3x 30-minute shift changeovers, the work day includes 22.5 hours instead of 24 hours.
(22.5 hours x 60 minutes) 1350 minutes ÷ 150 = 9 minutes
So, the customer demand Takt Time is 9 minutes per article.
Therefore, the team on the plant floor must produce one unit every 8 minutes to meet customer demand and the continuous order flow. If the team can run at a faster Takt Time, such as 4.5 minutes per article, the company can bring more products to the market within the same time period (a week, a month, a day, etc.)
Why Takt Time Metric Must be Low
As part of OEE metrics, the ideal goal is to run a Takt Time as low as possible. This is why you should optimize your operational processes –it’ll ensure a faster production line and output.
A low Takt Time metric includes many benefits, such as high efficiencies and high customer satisfaction as the demand of customers is met. It also reflects positively on the available article quantity and company revenues.
Major Causes of Long Takt Time
Unfortunately, that’s not always the case. Sometimes, a production line can run at a slow manufacturing time. What causes this?
- Work process disruption – For example, if there’s a power outage affecting the plant
- Limited access to raw materials – The rate of deliverables is also based on raw material unavailability.
- Lack of reliable data: Failing to collect accurate manufacturing time metrics or demand data will render Takt Time calculations ineffective.
- Lack of dependable vendors or suppliers – As a vital part of the supply chain, if they’re unable to meet company demand, it can affect production output.
- Unplanned production breaks – Equipment breakdowns, natural disasters, and worker downtime without any backups will cause unplanned production breaks.
How Do You Eliminate Long Takt Times?
In order to address high Takt Times value and slow production line output, a company must identify the real cause of the delay by addressing the following questions:
Why is my total manufacturing time longer than other same-size companies? How can they produce the same amount of work in a shorter timeframe?
Lean Manufacturing & Boosting Takt Time Value
The lean six sigma approach involves cutting out all forms of waste, eliminating what doesn’t add any value to your process. You’ll have to establish new rigorous standards that will assure customers of your product’s quality and continue to meet demand.
Lean six sigma is a very vital tool for this purpose if you’re looking to build or establish fast, efficient, and precise production lines that will lead to shorter Takt Times and high productivity.
Using Smaller Takt Or Tasks
Consider splitting the tasks that result in long Takt Time into smaller, bite-sized intervals that you’ll use to measure your progress. This way, the production line keeps moving and isn’t held up by backlogs of time-demanding tasks.
Assess Team Capacity & Takt Stations
A third strategy would be to reassess the time assumptions and workers’ capacity. Sometimes, a new perspective on time allocation and capacity can improve Takt Time.
For instance, instead of assuming –according to the initial takt time– that your firm needs a 9 minute Takt Time (based on the example above) for one unit, you can simply switch from a linear process and use a lateral one that involves installing more workstations instead of one.
Then, allocate the appropriate cycle time (see below for more) for each phase of the product creation, and let the stations do their work. This way, you’ll be able to meet up with demand and fill the quantity of units required faster.
To help you understand this, here’s a practical example: Imagine that instead of just one workstation, you have 9 more. You can easily cut and balance each phase’s cycle time for efficiency –if the average cycle time was 3 minutes, you can cut it down to 1.5-2 minutes max – so that the product can move on to the next phase.
The only challenge is the need for additional resources or manpower. But if you’ve trained your staff well, some of them can easily be deployed to the new stations where they can oversee the process. This way, you can get all your daily output done in 10% time it would normally take to meet customer demand.
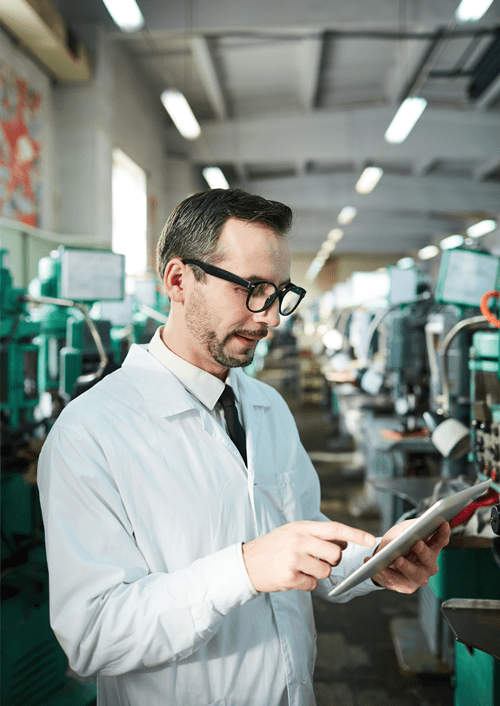
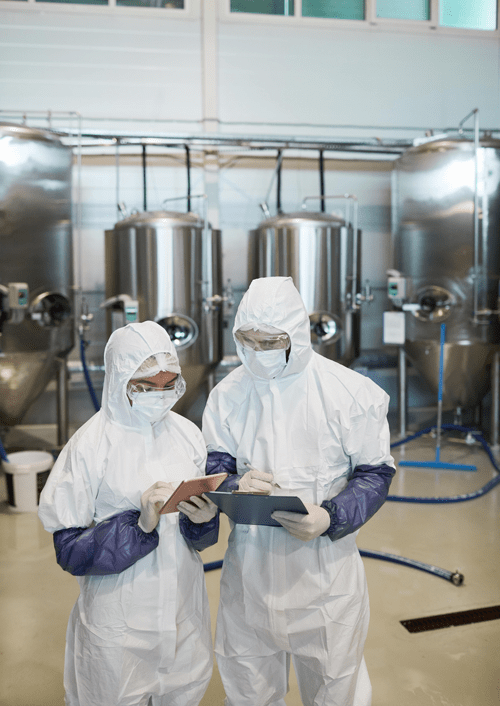
What is Cycle Time?
Many people confuse Takt Time with cycle time. They are two different things, even though they are both parts of a larger process. Cycle time is the length of time needed to finish a part of the process. For example, if the Takt Time for producing a pair of shoes is 2 minutes, one of the cycle times is the time it’ll take for the machine to apply the glue to the sole.
In the 2 minutes that it takes to produce the shoe, the various processes required to make the whole shoe have different cycle times. So, cycle times are usually subsets of a Takt Time.
Summarily, total cycle time = 1 Takt Time.
What is Lead Time?
This is the time interval between initiating a process and completing it. For example, the time between ordering a new vehicle and delivery is usually between 14 and 42 days. So, the time spent on doing the actual work, like constructing the car parts, assembling the car, testing it for quality issues, and finally delivering the complete vehicle, is known as lead time.
Takt Time Benefits
Fine-tuning Takt Time can drive a lot of benefits:
- The company can meet and satisfy customer demand more easily
- It helps with data collection and measuring your progress
- It’s easier to calculate time and resource expenditure
- It helps minimize wastage
- It can improve business operations and production lines
- Improving available production time allows you to access and fulfill demand in higher volumes
- It can improve productivity
- It contributes to better performance from employees
- It allows you to maintain a sustainable production and output rate
Conclusion
If your business operations are lacking and your delivery times seem long or inconsistent, Takt Time can help bring things under control. With proper implementation, it’s easier to determine how many product units your customers need per day, week, month, or even quarter, and meet those demands.
Think of it as a tool that helps shift your company’s direction, placing you on the right path for profits and prestige.