Manufacturers have an incentive to reduce changeover times. Dead periods between the production of one good and the manufacturing of another represent a significant cost. Unfortunately, effective changeover process management is an oft-overlooked aspect of doing business. As such, changeover times can vary wildly.
What Is Changeover Time?
How firms measure changeover time depends significantly on their industry. However, in general, it is defined as the time elapsed between the final item on the last production run and the next item on the new run, so long as it meets quality standards. If the new run does not meet quality control standards, the changeover is not complete.
Changing one manufacturing process to another eats into efficiency. Even if it only requires an hour a day to perform, that still equates to seven hours a week (assuming no downtime), or nearly sixteen days per year.
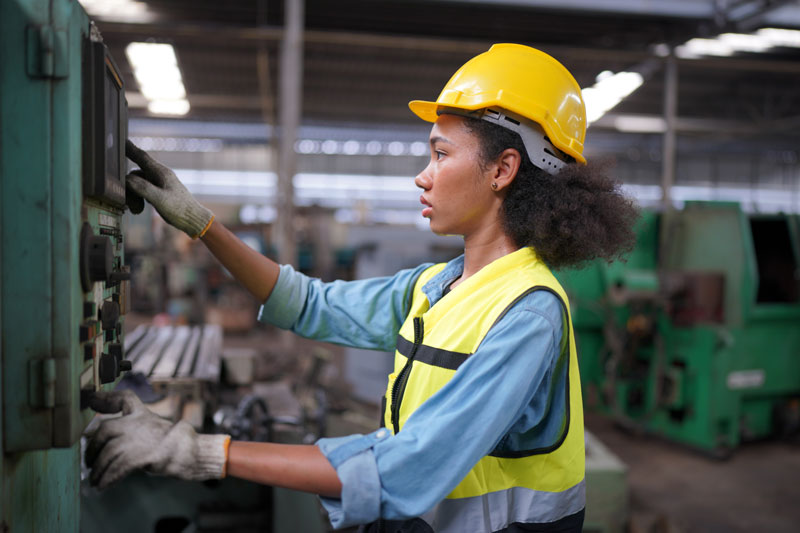
Set Up Time Versus Changeover Time
Manufacturers sometimes use set up and changeover times interchangeably. However, they refer to different concepts. Set up time is a subcomponent of changeover time. It refers to the amount of time spent preparing equipment to accept new production processes. Changeover time refers to the entire process, including clean up, set up, and start up.
How To Reduce Changeover Times
Reducing changeover times is possible, but it requires clearly understanding your current changeover process and an ability to achieve continuous improvement.
In the human realm, there are many non technical improvements to be made. Quick wins include coaching teams to look for easy process improvements, better defining roles, allowing for greater accountability, and creating a set of work instructions. Teams can then move to the next phase of retrieving all necessary parts before the changeover starts, avoiding unnecessary movement of equipment, and marking preferred settings on machinery.
Companies also need to make technical improvements to move towards greater efficiency, including installing quick-release mechanisms and modularizing equipment. This is an iterative process that lean manufacturing uses to reduce waste, cut the number of changeover steps, and improve efficiency.
The most accepted best practice for cutting changeover times is the single minute exchange of die (SMED) process. SMED adoption allows firms to cut changeover times below ten minutes. Pioneers of the technique, such as Shigeo Shingo, were able to slash times by a factor of twenty across multiple verticals in historical settings.
Under SMED, engineers break up the changeover process into a series of steps or a sequenced list called elements. The goal of the SMED approach is to remove these elements from the changeover process so that they become external to it, and then streamline other changes so that they can be done more rapidly when tooling changes are required.
Some firms differentiate between internal and external changeovers. Internal changeover is the time elapsed between the processing of the last piece of the previous run and the first piece of the next. External changeover, on the other hand, represents the amount of time that workers spend preparing before the exchange of dies and the finalization of changeover activities after the new run begins.
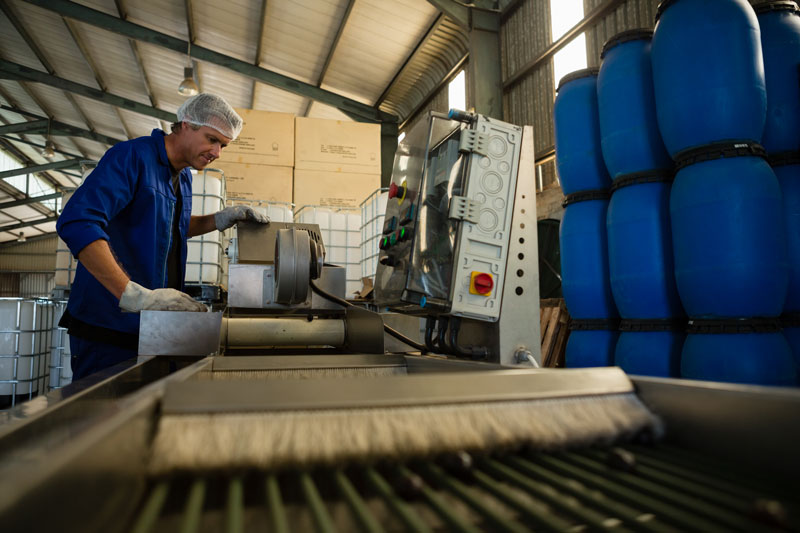
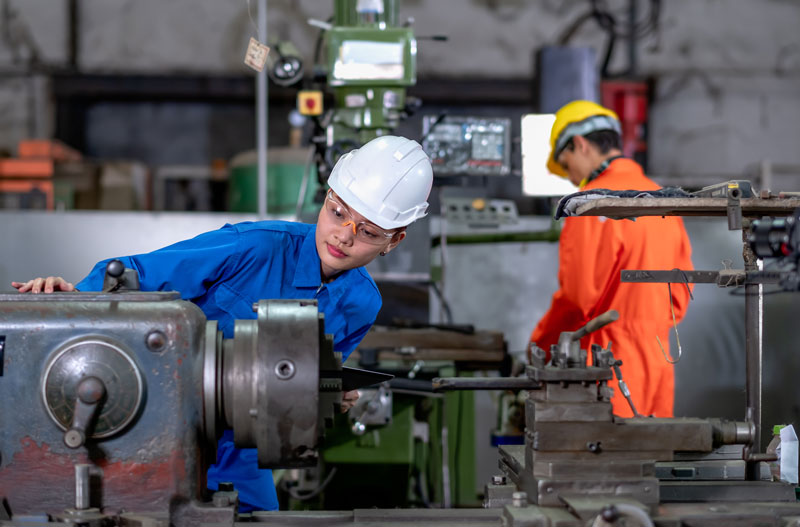
Benefits Of Reducing Changeover Times
Reducing changeover times offers companies a host of benefits. These include:
React Better To Changes In Customer Demand
Manufacturers need to maintain customer satisfaction. To do that, they need to eliminate as many changeover steps as possible to facilitate improved changeover times just in case demand changes.
Unlock More Value Added From Production Runs
Long changeovers are a drag on company profits. However, moving towards a single minute exchange of dies can boost capital efficiency tremendously. Companies can get more done in less time, enhancing their production process.
Reduce Batch Size
Large batch sizes bring costs down, but they eliminate smaller customer orders. Reducing changeover time allows firms to cut production batch size and improve customer satisfaction. At the same time, manufacturers can also cut work in process (WIP), and inventory.
Reduced Lead Times
In some cases, reducing changeover time can actually allow firms to cut their lead-time estimates. Sales teams can then quote more competitively and back up their promises with real time metrics.
Work Instructions For Changeover Procedures
Before you begin making material changes to your changeover time, it is a good idea to audit the current state of your processes and then document your baseline. Then you have a point of comparison.
Achieving best practice typically takes the following format:
Step 1: Break Down Your Changeover Process Into Discrete Elements
Commonly accepted categories include clean-up, set-up, and start-up.
Step 2: Document The Process
Next, you’ll want to quickly document changeover procedures. Observe or record your current operations using known settings. If necessary, video the process.
Step 3: Break Down Each Production Process Into Smaller Steps
Along the lines of SMED, you will want to break down all of the remaining elements that contribute to your changeover time. Consider each of the remaining steps as an individual action and then ask whether it could be done differently.
Step 4: Track Cycle Time
Next, record how long it takes you to perform each step as well as the entire changeover process. Each time you perform a new changeover, you can see where you have lost time and make the necessary program changes.
Step 5: Repeat And Improve
Once you have standardized and documented your processes, you can start making real improvements. In many cases, you will see opportunities to move aspects of the process into the external category, reducing the amount of time your manufacturing facility is offline. You can also look for opportunities to reduce errors and streamline internal processes before updating workers on the changes.
At the end of the process, you should be able to slash planned downtime. You may also reduce production batch sizes to levels ideally suited by your customers.
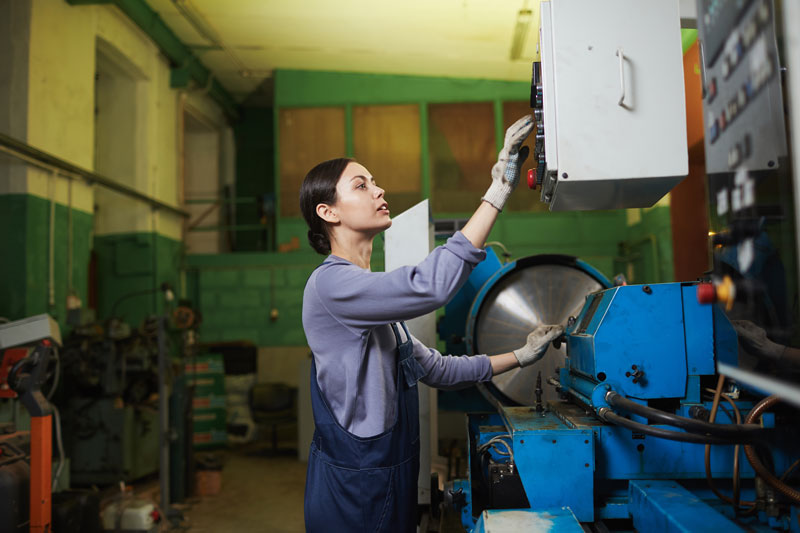
Conclusion
The benefits of reducing changeover time are significant. By breaking the process into steps called elements, you can improve efficiency, cut your costs, and cut waste.
PerformOEE™ users, CooperVision, Hamble, Southampton UK can attest to this. Initially engaging in a Software Pilot, CooperVision were looking for alternative ways to meet their rapidly growing market share. They knew that they needed to find a way to increase their capacity from their existing resources but didn’t know where to start.
Initially installed on only one production line, the software immediately confirmed that there were huge variations in the time it took to complete a batch change on that line. By reorganizing their teams and working with them to remove the variation, CooperVision succeeded in setting a standard time for their batch changeovers which in turn resulted in 5% more lenses coming off the line.
This gave them an immediate increase in their overall equipment effectiveness (OEE) score and also improved their single minute exchange of dies (SMED) scores due to better monitoring on the line.
Ultimately, reducing changeover time lets you better serve your customers through better lead times and lower-priced output.
"Applying the “One Team” principle led to better organization of our teams – the shift leaders for Production, MSE and Asset Care share a single Control Room, where critical modules and bottlenecks are monitored and highlighted in real-time...
We are able to review the lines, compare them and work on them to keep the yields going." - Rob George, CooperVision UK