OEEsystems + MaintMaster
Accelerating Manufacturing Excellence Two Industry Leaders Join Forces.

Control your process by highlighting issues in real-time, enabling the right response.

Powerful Control, Visibility and Root Cause Analysis to drive Continuous Improvement.

Industry 4.0 & Smart Factory IIoT that delivers Cultural & Digital Transformation in your Manufacturing Operations.
Smart Factory OEE Software
PerformOEE™ Smart Factory Software is a Smart Factory OEE Software Solution used by the world’s leading progressive manufacturing companies. It is their preferred IIoT application for managing real-time production performance improvement.
PerformOEE™ can be used for Discrete, Process and Continuous manufacturing processes across all industries. Our OEE Software is suitable for all users within your business, from operators on the shop floor to those at senior management level. Our Quality Compliance Checklists, Dashboards and Reports are perfect for those operating in regulatory environments.











View production progress in real-time as you work
Track important information & visualise results
Reduce costs & increase overall profitabilty
Drive continuous manufacturing improvement
We Are The OEE People
We work with the world’s most progressive manufacturing companies to increase capacity, reduce costs and drive continuous improvement. Our unique record of combining our Smart Factory OEE Software, PerformOEE™, with our Science of Manufacturing Methodology delivers real-time visibility, analysis and control of your manufacturing performance.
That makes us The OEE People.
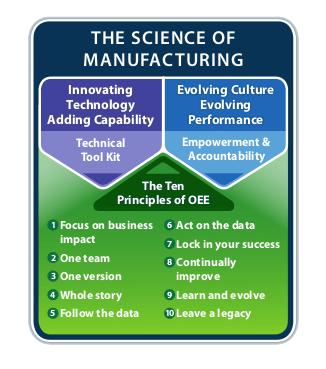
Transformational Results
Output
Yield
The Science of Manufacturing
Our Science of Manufacturing Methodology, a set of ten proven principles combining technical innovation with a focus on people and culture, is used to deliver successful continuous improvement programs.
Presented as an easy to read pocket guide, our methodology, combined with PerformOEE™ Smart Factory Software,can help you achieve step-change business performance improvement and tangible business impacts.
OEE Software Testimonials

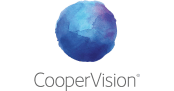
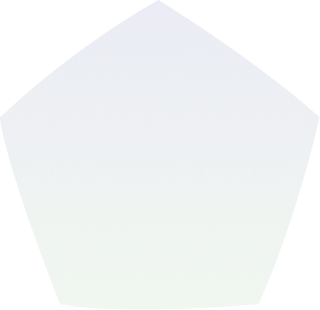
Capterra Client Reviews
Overall Capterra Rating
What is OEE (Overall Equipment Effectiveness)?
Overall Equipment Effectiveness (OEE) is a measure of how well a manufacturing process is used in regard to the total potential. It shows the percentage of productive production time at work. OEE is the most effective metric to identify gaps, determine progress and improve the productivity of manufacturing equipment, and eliminate waste. OEE provides insight on how to better ensure quality control.
What Does OEE Mean?
Overall equipment effectiveness (OEE) is a principal standard for the measurement of manufacturing productivity. It can help you to gain a better understanding of your plant floor metrics so that you can improve the quality score of your manufacturing performance by analyzing and resolving process defects such as reduced yield, availability loss, substandard materials, and much more to improve upon your performance score with the help of world-class OEE analysis.
OEE is one of the best meters for discrete manufacturers optimizing their production process. Once you are able to accurately calculate OEE, you can discover how to improve the OEE score of your machinery and maximize its production output.
The Overall Definition of OEE
OEE is the measure of the performance of assets against their future potential. It estimates production capacity – specifically physical materials, time, and physical assets – by measuring the usage of manufacturing resources to indicate the gap between the real and intended performance.
OEE has become a commonly cited key performance indicator (KPI) and manufacturing best practice. It offers useful details to improve systems and get your production to a standard that is considered world-class. OEE (when used with correct accuracy) helps you understand your production process.
Why is OEE Important?
OEE offers solutions to improve your manufacturing time and gain a better insight when setting a real-time production target by measuring manufacturing productivity and preventing any potential loss factors that could impact your performance calculation.
Using the visualization process of all losses from production lines or machinery, OEE not only indicates what was produced from resources but also shows what they could have produced. OEE is not only a performance indicator but also a more important continuous improvement tool that allows us to eradicate waste and target “the six big losses”, which exist in almost every manufacturing plant.
Understanding OEE
OEE is a complete performance measurement that helps focus improvement on the most critical and common areas of productivity decline. The concept of the six big losses has direct ties with TPM (Total Productive Maintenance).
OEE shows us the ways in which we use our machinery and production facilities effectively. It helps demonstrate a very effective method of delivering quality products to our customers, whilst simultaneously displaying methods of eliminating waste.
Schedule losses are not taken into account for OEE, as measuring OEE is redundant when production doesn’t necessarily run. Schedule losses are used in calculating TEEP (Total Effective Equipment Performance).
What is a Good OEE Score?
OEE scores are always presented as a percentage. They provide additional useful information regarding the ability to compare different shifts in the same organization. OEE is calculated as the ratio of your manufacturing plant run time to planned production time.
A scoring of 100% for OEE signifies perfect production – your manufacturing line develops great parts at maximum speed with no possible failure. Upon achieving 100% OEE, it signifies that your organization was able to achieve full production in a flawless manner.
An OEE score above 85% is master class, with offerings of 90% availability to 95% performance to 99% quality KPIs. OEE is a reference for the leading standards in the manufacturing process.
Overall Equipment Effectiveness: Terms to Know
Before discussing your overall equipment efficiency and how to calculate it, there are certain important terms you should keep in mind: Availability, Performance, and Quality.
Availability:
Availability refers to scheduled and unplanned stops involving production. These losses are known as availability losses, and this measure tracks uptime and calculates the percentage of time. Obtaining an availability score that of 100% would mean that your process is running at optimal output, and there is no availability loss.
Availability is also to do with the percentage of running time that is available to production. In a category of loss, unprepared and planned stops are losses. Unplanned stoppage is a period during which equipment has been scheduled for production, but is not running due to unplanned events.
Planned stops include changeover adjustment of equipment cleaning, planned production maintenance, and quality inspection. Paid holidays, meetings, toolbox presentations, etc., are also categorized here.
However, we can’t categorize planned activities – maintenance shutdowns and major plant repairs – as an available loss. Thus, we are unable to use those in OEE calculations, and they are necessary to avoid.
In OEE calculations, availability starts at 100% less planned downtime; a gross operating time. Planned breakdown period, or planning factor, includes planned maintenance activities and planned gaps in the production schedule. Moreover, the availability/removal of breakdowns, as well as reduction of setup and adjustment losses could benefit the provision and availability rate.
In the case of something like no collection, there will be no planned downtimes in a schedule, and no incentives to find better ways to cut or eliminate setup or transition time. But if they were not included in planned downtime, those numbers could skew this reading.
Performance:
Performance is the throughput of the plant during a running period compared to the maximal throughput. Performance loss is classified with micropause and slow cycles. Micro stops are repetitive and can have the operator unaware of their impact. Slow cycles may be caused by dirt or worn-out slacklines, faulty lubricant or poor material selection, poor environmental conditions, incorrect settings, or human factors. It is inevitable that when equipment runs slower that your total count of units produced will suffer and you will not be able to achieve maximum throughput.
Performance is sometimes named ‘process rate’. This is the speed the system has calculated compared to the design (the maximum possible) speed measured. Losses resulting from wasted performance should be called performance losses. Obtaining an accurate performance score will help greatly when calculating your overall OEE score.
This system is based on the removal of losses from operation, such as running slower than a machine for idle and minor stops, which will affect your reduced speed within the calculation and could end up resulting in a low score.
Quality:
Quality measures and defines the percentage of produced excellent parts. This measure can help establish an average of defective units from the top quality. Manufacturers that are not on target for certain quality standards represent quality losses. 100% quality means you can achieve perfect production with zero defects. This part of overall equipment effectiveness provides information about where there can be defects., and will be reflected as such within your quality score.
Production rejects occur as defective products. OEE tests the quality in real terms by evaluating the percentage of actual production throughput which exceeds customer specifications exactly the first time. The aim is to reduce your production rejects as much as possible in order to reach a perfect production run and eliminate and process defects.
Producers tend to follow them the most after changeovers, such as suboptimal changeovers or equipment that needs the ‘warm-up cycle’, and equipment that inherently creates waste after start-ups, which can be categorized in your quality loss.
Quality also represents loss of quality production and losses during the startup/shut down procedure. As a KPI of business, it represents a measure that can identify opportunities and drive effective improvements. Learn to evaluate the full productivity of an industrial plant and encourage executives to utilize OEE to identify opportunities and deliver real improvements in the workplace.
Where to Start with OEE?
OEE analyses start from Production Time, which is when the plant is operational in terms of availability to production. Then, subtract the time taken for planning a stop. That includes all circumstances that can no longer be in the analysis because the unit cannot be run. This means breakages, lunches, and planned maintenance. The time remaining is referred to as planned time of production. OEE commences with planned process time and then subtracts all production loss, and those are then targets for improvement work.
How Do You Calculate OEE?
Overall Equipment Effectiveness is the relationship between what will actually be produced and what can be produced. OEE is usually calculated during the first week or at the end of the month. More frequent measurements will affect the calculation.
It is important to distinguish between efficiency and efficacy. For example, if you manufacture machines that make 80 products every hour, then in comparison, the operation would make 80% of that power. Effectiveness increases for two employees by 25%, while labor efficiency declines on a labor-based basis. OEE measures the number of operating units, energy, and materials that are needed to obtain this 80%.
OEE multiplies availability, performance, and quality. Measurement starts with availability and performance of assets. Quality is also determined by dividing the number of usable units produced by the total starting units.
I.E., the quality is 0.975 – or 97 – an OEE % – for a machine that lasted for 11 hours. The measurement was based on an asset that ran for 12 hours, with a maximum production rate of 1,000 units per hour.
The easiest way to calculate overall equipment effectiveness (OEE) is by multiplying the number of good parts produced (good count) by the ideal duration of production (ideal cycle). Then divide this number by scheduled production time.
But the preferred way to calculate OEE is mathematically similar to the simple formula above and provides a richer understanding of waste in the manufacturing process by dividing it into three losses.
OEE reflects all three components – availability, performance, and quality. It is easy to calculate: availability % x performance % x quality % = OEE %.
OEE mixes these factors into a single KPI. It is not a perfect formula, and few firms should trade an availability increase by 5% for quality loss. However, OEE is the best way to compare. The key is clearly to see that improvement is not just the goal, but how improvements can be achieved.
This advanced OEE calculation takes three factors into consideration. Then each factor must be calculated separately.
OEE Example
In this hypothetical example, the manufacturing process of a spoon-producing plant, the plant produces 600 spoons in 60 minutes in ideal conditions at 1 spoon per second. Due to the lunch hour and the downtime, the productive period was only 240 minutes for this particular shift. For this time frame, they would have produced 14,100 units. This yields the following numbers:
Performance = Total number x Ideal cycle time : Run time : Planned Production = 14100 units x 1 second : Unit units produced by.
How to Use OEE to Measure Manufacturing Productivity
The OEE measurement for the effectiveness of the total equipment is used as a benchmark for comparing product production to industry standards. In short, overall equipment effectiveness is not only a great tool for managers but could also be extremely important to employees on the plant floor.
The plant floor metric OEE is used to measure productivity and other plant floor metrics. OEE can also be used to compare industry standards with other equipment or shifts at the same time and place.
Is OEE a KPI?
OEE is a key performance driver for any production plant. A high OEE score is a hallmark for an extremely efficient factory. A poor OEE score implies there is a hidden factory of used resources that are generating losses.
This could be the result of several contributing factors to your production processes. OEE will help to provide you with valuable data to discover how you can obtain a more stable production and make life easier for your machine operators.
How To Improve Your Overall Equipment Effectiveness Score
Only by working on the prevention of losses can OEE be improved. Equipment breakdown can be a direct consequence of reactive maintenance. Machines that do suffer from unscheduled downtime can make it hard to maintain in peak operation conditions, preventing optimal total units produced and increasing preventative maintenance. This goes to show that manufacturers need to use the proactive maintenance techniques that OEE offers to them.
How to Reduce Availability and Performance Losses
Find and deal with the conditions which cause unavailability first. Similarly, performance losses can be a major cause of production line failure. Performance loss is difficult to completely eliminate, but can be reduced:
Reduce Idle/Minor Stops
Idling and minor stops are stops lasting for a few minutes. Many repeated ‘minor’ incidents, such as a faulty conveyor belt or a jammed component suddenly increasing over time increase loss. As a business makes progress at using and tracking problems there are also needs for addressing these improvements in normal operating practices and preparing affected employees. It helps to prevent another similar problem from recurring in the future.
Reduce Equipment Downtime
Unexpected breakdowns leading to unplanned downtime are the largest one-way source of productivity loss. This information can help the team to decrease downtime by starting with the most common downtime causes. Optimizing equipment failure may contribute to decreasing downtime and reducing production times by addressing equipment-related causes. Utilizing OEE can help to avoid common and critical matters that are costing your organization time and money and can also help your organization eliminate common maintenance problems.
Shorten Time Spent on Setup/Adjustments
These take place during the transition phase or adjustment period of machines, e.g. after upgrading a tooling process to adapt to a different product. The time of shutting down is also considered during preventive maintenance. Additional strategies include optimizing the plant’s downtime and reducing the loss from setting loss adjustments using reduced.